AI-Driven Quality Control: Reduce Errors by 30% in US Manufacturing
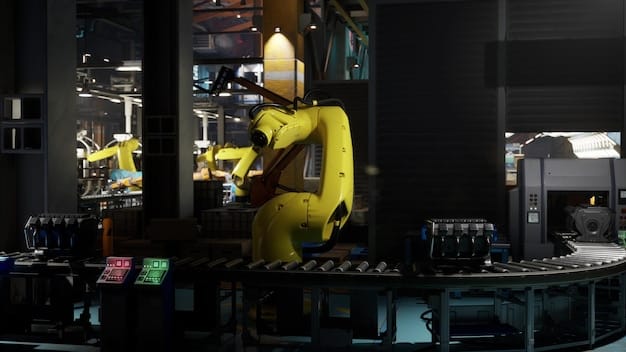
AI-driven quality control tools are revolutionizing US manufacturing by leveraging advanced algorithms and data analysis to identify and rectify defects, aiming to reduce errors by 30%, improve product consistency, and streamline production processes.
In today’s competitive manufacturing landscape, precision and efficiency are paramount. Reduce Errors by 30%: AI-Driven Quality Control Tools for US Manufacturing are emerging as game-changers, offering unprecedented capabilities to minimize defects, optimize processes, and boost overall productivity.
The Imperative of Quality Control in US Manufacturing
Quality control is the backbone of any successful manufacturing operation. In the US, maintaining high standards is not just about reputation; it’s about regulatory compliance, customer satisfaction, and ultimately, profitability. Traditional methods, however, often fall short in addressing the complexities of modern production lines.
Human inspectors are prone to fatigue and subjectivity, leading to inconsistencies and missed defects. Manual processes are also time-consuming and expensive, especially when dealing with high-volume production. So, how can manufacturers overcome these challenges?
The Limitations of Traditional Quality Control
Traditional quality control methods rely heavily on manual inspection, statistical sampling, and periodic testing. These approaches are often reactive rather than proactive, addressing issues only after they arise. This can lead to:
- Increased scrap and rework costs.
- Delayed production schedules.
- Damaged customer relationships.
- Difficulty in identifying the root causes of defects.
The integration of AI-driven quality control tools offers a transformative solution by providing real-time monitoring, predictive analysis, and automated defect detection.
How AI is Transforming Quality Control
Artificial intelligence is no longer a futuristic concept; it’s a practical solution being implemented across various industries, including manufacturing. AI-powered quality control tools leverage machine learning, computer vision, and data analytics to automate and enhance inspection processes. This leads to more accurate, efficient, and cost-effective quality assurance.
The core of AI’s transformative power lies in its ability to analyze vast amounts of data and identify patterns that would be impossible for humans to detect. Let’s delve into some key benefits.
Key Benefits of AI in Quality Control
AI offers a range of benefits that address the limitations of traditional quality control methods.
- Real-time defect detection: AI systems can monitor production lines continuously, identifying defects as they occur.
- Automated inspection: AI algorithms can automate visual inspection tasks, reducing the need for manual labor.
- Predictive analysis: AI can analyze historical data to predict potential defects and proactively address them.
- Improved consistency: AI systems provide consistent and objective assessments, eliminating human subjectivity.
By leveraging these capabilities, manufacturers can significantly reduce errors, improve product quality, and increase overall efficiency.
Understanding AI-Driven Quality Control Tools
AI-driven quality control tools encompass a variety of technologies designed to automate and enhance inspection processes. These tools utilize machine learning algorithms to analyze data, identify defects, and predict potential quality issues. Understanding the different types of tools available is crucial for selecting the right solution for your manufacturing needs.
These tools can be broadly categorized into computer vision systems, machine learning models, and data analytics platforms. Although each category of AI has its strength it is not common to see applications using all of them to achieve the best results.
Types of AI Quality Control Tools
Let’s explore the various types of AI-driven quality control tools.
- Computer vision systems: Use cameras and image processing algorithms to visually inspect products for defects.
- Machine learning models: Analyze data from sensors and production systems to identify patterns and predict potential issues.
- Data analytics platforms: Provide insights into production processes, enabling manufacturers to optimize performance and reduce errors.
Each of these tools offers unique capabilities that can be tailored to specific manufacturing applications. This allows for very specific improvements in otherwise very complex manufacturing processes.
Implementing AI in Your Manufacturing Process
Implementing AI-driven quality control tools requires careful planning and execution. It’s essential to assess your current processes, identify areas for improvement, and select the right technologies to meet your specific needs. A phased approach, starting with pilot projects, can help ensure a smooth transition.
One of the most important requirements is to have your system feed real data. In reality, a lot of effort is put into providing the AI with useful information that it can use to achieve the desired results.
Steps for Successful Implementation
Below are key steps to ensure a successful AI implementation.
- Assess your current processes: Identify pain points and areas where AI can provide the most value.
- Select the right tools: Choose AI technologies that align with your specific needs and requirements.
- Train your team: Provide training and support to ensure your team can effectively use and maintain the AI systems.
- Monitor and optimize: Continuously monitor the performance of your AI systems and make adjustments as needed.
While it may seem daunting to implement AI into your operation, it can provide long-term improvements to the cost of production by reducing the defect output.
Case Studies: AI Success Stories in US Manufacturing
Several US manufacturers have already seen significant improvements in product quality and efficiency by implementing AI-driven quality control tools. These success stories demonstrate the potential of AI to transform manufacturing operations.
These companies have used AI to reduce defects, improve production efficiency, and enhance overall profitability. In addition, brand perception typically jumps as people recognize a higher quality in the output.
Examples of AI Implementation Success
Here are some real-world examples of AI improving the manufacturing process.
Improving Quality Control: AI in Action
- Automotive Industry: An automotive manufacturer used computer vision to automate the inspection of welds, reducing defects by 40%.
- Electronics Manufacturing: An electronics company implemented machine learning models to predict component failures, preventing costly downtime.
- Food and Beverage: A food processing plant used data analytics to optimize production processes, reducing waste and improving product consistency.
The case studies are clear that AI can be a crucial component of future manufacturing and these are just areas that it can be implemented in. As the adoption of AI increases, the competition may be forced to get on board or risk falling behind other companies in their output quality.
The Future of Quality Control: Trends and Predictions
The future of quality control in US manufacturing will be increasingly driven by AI. As AI technologies continue to evolve, we can expect to see even more sophisticated and effective quality control solutions. This includes advancements in computer vision, machine learning, and data analytics.
AI is expected to also become more ubiquitous in the manufacturing process and a larger set of operators will have a strong understanding of its purpose.
Emerging Trends in AI Quality Control
As the times change, there are bound to be changes in the way AI and future manufacturing function.
- Edge computing: AI systems will be deployed closer to the production line, enabling real-time decision-making.
- Explainable AI: AI algorithms will become more transparent, providing insights into how they make decisions.
- Generative AI: AI will be used to design and optimize manufacturing processes, improving efficiency and reducing waste.
By staying ahead of these trends, manufacturers can leverage the full potential of AI to drive innovation and improve competitiveness.
Key Point | Brief Description |
---|---|
🤖 AI-Driven Quality Control | AI tools enhance manufacturing precision & efficiency. |
📈 Error Reduction | Aims to reduce manufacturing errors by 30%. |
🏭 US Manufacturing | Focuses on improving quality control in US factories. |
🔍 Predictive Analytics | AI predicts potential issues for proactive solutions. |
Frequently Asked Questions
▼
These tools utilize artificial intelligence to automate and enhance inspection processes in manufacturing. AI can reduce the time in checking all components during a manufacturing process.
▼
AI systems can analyze data, identify defects, and predict potential quality issues, leading to a significant reduction in errors in the manufacturing process.
▼
Tools such as computer vision systems, machine learning models, and data analytics platforms all contribute to automating the manufacturing process.
▼
Implementing AI requires careful planning and a phased approach, starting with pilot projects to ensure a smooth transition as there may be complex training elements.
▼
The automotive industry uses it to inspect welds, electronics companies predict component failures, and food processing plants optimize production, each leading to measurable improvements.
Conclusion
In conclusion, AI-Driven Quality Control Tools for US Manufacturing offer a promising path to reduce errors, improve product consistency, and boost overall efficiency. By embracing these technologies, manufacturers can stay ahead of the competition and meet the ever-increasing demands of the modern market.