Streamline Operations with AI: Automation Tools for US Manufacturing
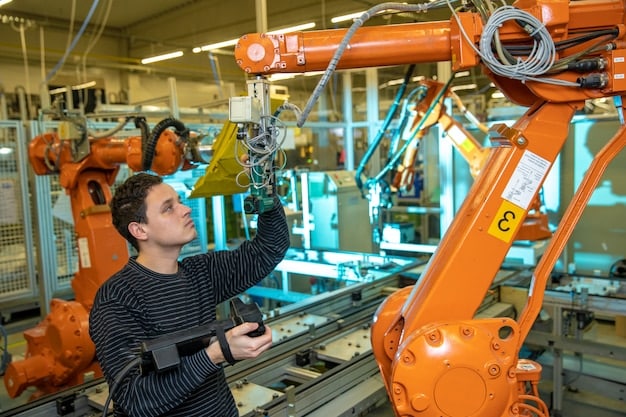
Streamline Operations: Implementing AI-Driven Automation Tools in Your US Manufacturing Plant focuses on deploying AI-powered solutions to optimize processes, reduce costs, and enhance efficiency in US manufacturing facilities, leading to increased productivity and competitiveness.
In today’s competitive landscape, manufacturers in the United States are constantly seeking ways to improve efficiency and reduce costs. Streamline Operations: Implementing AI-Driven Automation Tools in Your US Manufacturing Plant offers a pathway to achieving these goals by leveraging the power of artificial intelligence.
Understanding the Current State of US Manufacturing
The US manufacturing sector is facing increasing pressure to innovate and adapt to global competition. Understanding the current state involves recognizing the challenges and opportunities that AI can address.
Adopting AI and automation is no longer a luxury, but a necessity for US manufacturers aiming to maintain a competitive edge. The sector is characterized by a mix of traditional processes and emerging technologies.
Key Challenges in US Manufacturing
Several persistent challenges impact the efficiency and productivity of US manufacturing plants.
- Labor Shortages: Finding and retaining skilled workers is a significant issue.
- Supply Chain Disruptions: Unpredictable events can cause delays and increase costs.
- Rising Operational Costs: Energy, materials, and labor expenses are constantly increasing.
- Need for Increased Efficiency: Optimizing production processes is crucial for profitability.
These challenges can be addressed by strategically implementing AI-driven automation tools that can augment human capabilities, predict disruptions, and optimize resource allocation.
Opportunities for AI Implementation
Despite the challenges, there are numerous opportunities for AI to transform US manufacturing.
- Predictive Maintenance: AI can analyze data to predict equipment failures and schedule maintenance proactively.
- Quality Control: AI-powered vision systems can detect defects more accurately than human inspectors.
- Process Optimization: AI algorithms can optimize production schedules and resource allocation.
- Supply Chain Management: AI can improve forecasting and risk management.
By capitalizing on these opportunities, manufacturers can significantly improve their operational effectiveness and reduce waste.
In conclusion, recognizing the present challenges and embracing the opportunities presented by AI is crucial for modernizing US manufacturing plants and ensuring their long-term viability.
Identifying Key Areas for AI Automation
To effectively implement AI, manufacturers should identify specific areas within their operations that can benefit most from automation. Targeting key processes can lead to significant improvements.
Identifying these areas requires a thorough assessment of current workflows and pain points. A strategic approach can help prioritize the implementation of AI-driven solutions.
Production Line Optimization
The production line is often the heart of a manufacturing plant, and optimizing it can have a substantial impact.
- AI-Powered Robotics: Robots can perform repetitive tasks with greater speed and precision.
- Real-Time Monitoring: AI can monitor production in real-time, identifying bottlenecks and inefficiencies.
- Automated Adjustments: AI can automatically adjust machine settings to optimize performance.
Implementing AI on the production line can lead to increased throughput, reduced errors, and improved overall efficiency.
Supply Chain and Logistics
Managing the supply chain is a complex task, but AI can significantly streamline these processes.
- Demand Forecasting: AI can analyze historical data to predict future demand more accurately.
- Inventory Management: AI can optimize inventory levels, reducing storage costs and minimizing waste.
- Logistics Optimization: AI can optimize delivery routes and schedules, reducing transportation costs.
By automating supply chain and logistics, manufacturers can ensure a more reliable and cost-effective flow of materials and finished goods.
In summary, identifying key areas for AI automation involves targeting specific processes that can benefit most from AI, such as production line optimization and enhancements to supply chain logistics.
Selecting the Right AI Tools for Your Plant
Choosing the right AI tools is crucial for successful implementation. The selection process should be based on the specific needs and objectives of the manufacturing plant.
It’s important to consider a range of factors, including the cost, functionality, and integration capabilities of each tool. A well-informed decision can ensure a positive return on investment.
Types of AI Tools Available
Several types of AI tools are available for manufacturing, each designed for specific applications.
- Machine Learning Platforms: These platforms provide the tools and infrastructure for building and deploying AI models.
- Computer Vision Systems: These systems use cameras and AI algorithms to analyze images and videos for quality control and other applications.
- Natural Language Processing (NLP) Tools: These tools enable machines to understand and respond to human language.
Understanding the different types of AI tools can help manufacturers choose the ones that best fit their needs.
Factors to Consider When Choosing AI Tools
When evaluating AI tools, several factors should be taken into account.
- Scalability: The tool should be able to handle increasing data volumes and user loads.
- Integration: The tool should integrate seamlessly with existing systems and workflows.
- Ease of Use: The tool should be user-friendly and require minimal training.
- Cost: The total cost of ownership, including licensing, implementation, and maintenance, should be considered.
Carefully considering these factors can help manufacturers choose AI tools that are both effective and affordable.
In conclusion, selecting the right AI tools requires understanding the available options and carefully considering the specific needs and objectives of the manufacturing plant.
Implementing AI-Driven Automation: A Step-by-Step Guide
Implementing AI-driven automation requires a structured approach to ensure success. A step-by-step guide can help manufacturers navigate the implementation process smoothly.
Following a systematic plan can minimize risks and maximize the benefits of AI automation. Each step should be carefully considered and executed.
Step 1: Assessment and Planning
The first step is to assess the current state of the manufacturing plant and develop a detailed plan.
- Identify Areas for Improvement: Pinpoint specific processes that can benefit from AI automation.
- Define Objectives: Set clear, measurable goals for the AI implementation.
- Develop a Roadmap: Create a detailed plan outlining the steps, timelines, and resources required.
A thorough assessment and planning phase is crucial for setting the stage for a successful AI implementation.
Step 2: Data Collection and Preparation
AI algorithms require high-quality data to function effectively. Collecting and preparing data is a critical step.
- Gather Relevant Data: Collect data from various sources, such as production machines, sensors, and databases.
- Clean and Preprocess Data: Ensure that the data is accurate, complete, and properly formatted.
- Create Training Datasets: Prepare the data for training AI models.
High-quality data is essential for training accurate and reliable AI models.
Step 3: Model Development and Training
The next step is to develop and train the AI models that will power the automation system.
- Choose Appropriate Algorithms: Select the AI algorithms that are best suited for the specific application.
- Train the Models: Use the prepared data to train the AI models.
- Evaluate Performance: Assess the accuracy and reliability of the models.
Effective model development and training are critical for ensuring that the AI system functions as intended.
In summary, implementing AI-driven automation involves a structured approach, beginning with an assessment and planning phase, followed by data collection and preparation, model development, and model training.
Overcoming Common Challenges in AI Implementation
Implementing AI in manufacturing is not without its challenges. Understanding and addressing these challenges is crucial for success.
Manufacturers may encounter technical, organizational, and cultural obstacles. Proactive strategies can help overcome these hurdles.
Data Quality and Availability
One of the most common challenges is ensuring the quality and availability of data.
Data quality is essential for training effective AI models. However, data in manufacturing plants is often noisy, incomplete, or inconsistent. Before training AI models, it is crucial to clean and validate the data. Additionally, manufacturers need to ensure that they have sufficient data to train their models. This may require investing in additional sensors or data collection systems.
Integration with Existing Systems
Integrating AI systems with existing manufacturing infrastructure can be complex.
Many manufacturing plants have legacy systems that are difficult to integrate with modern AI tools. To overcome this challenge, manufacturers may need to invest in middleware or APIs that can bridge the gap between old and new systems. It’s also essential to plan the integration carefully and test thoroughly to avoid disruptions to production.
Lack of Expertise
Another challenge is the lack of in-house expertise in AI and data science.
Implementing AI requires specialized knowledge and skills that many manufacturers do not possess internally. To address this, manufacturers can hire AI experts, train existing employees, or partner with external consultants or technology providers. Continuous learning and development are essential for keeping up with the rapidly evolving field of AI.
Overcoming these challenges requires a proactive and strategic approach. By addressing data quality issues, integrating systems effectively, and building internal expertise, manufacturers can successfully implement AI and realize its full potential.
Measuring the ROI of AI Automation in Manufacturing
Measuring the return on investment (ROI) is critical for justifying AI investments and ensuring that they are delivering the expected benefits. Establishing clear metrics and tracking performance are essential.
Tracking Key Performance Indicators (KPIs) can help manufacturers assess the impact of AI automation. Regular monitoring ensures ongoing improvements.
Key Performance Indicators (KPIs) to Track
Several KPIs can be used to measure the ROI of AI automation.
- Overall Equipment Effectiveness (OEE): Measures the efficiency and productivity of manufacturing equipment.
- Defect Rate: Tracks the percentage of defective products.
- Production Throughput: Measures the volume of products produced over a given period.
- Operational Costs: Tracks the expenses associated with running the manufacturing plant.
By tracking these KPIs, manufacturers can gain insights into the impact of AI automation on their operations.
Calculating the ROI of AI Automation
The ROI of AI automation can be calculated using the following formula:
ROI = (Benefits – Costs) / Costs
The benefits include increased production, reduced defects, and lower operational costs. The costs include the expenses associated with implementing and maintaining the AI system.
In conclusion, measuring the ROI of AI automation involves tracking key performance indicators and calculating the financial return on investment. Regularly monitoring performance ensures that AI investments are delivering the desired results.
Key Point | Brief Description |
---|---|
🏭 Automation Areas | Identifies key areas like production lines and supply chains for AI implementation. |
🛠️ AI Tool Selection | Highlights the importance of choosing appropriate AI tools based on plant needs. |
📊 ROI Measurement | Stresses tracking KPIs to measure the return on AI investments. |
⚙️ Implementation Steps | Provides a step-by-step approach to ensure a smooth AI implementation process. |
Frequently Asked Questions (FAQ)
▼
AI can improve efficiency by automating tasks, reduce costs through predictive maintenance, enhance product quality with AI-driven inspections, and optimize supply chain management. It can lead to increased productivity and profitability.
▼
AI-driven computer vision systems can automatically inspect products for defects, identifying flaws that human inspectors may miss. These systems can detect even minor issues, reducing the number of defective products reaching consumers.
▼
Common AI tools include machine learning platforms for predictive maintenance, computer vision systems for quality control, and natural language processing tools for streamlining communication and documentation processes. These tools are designed to enhance various aspects of manufacturing.
▼
Integrating AI can be complex, especially with legacy systems. It may require middleware or APIs to bridge the gap. Careful planning and thorough testing are essential to avoid disruptions. A phased approach often works best for managing this integration.
▼
The ROI timeframe varies depending on the specific AI applications and the scale of implementation. Some improvements may be seen immediately, while others may take several months to a year to fully materialize. Continuous monitoring is essential.
Conclusion
Implementing AI-driven automation tools offers a transformative opportunity for US manufacturing plants to streamline operations, enhance efficiency, and gain a competitive edge. By carefully assessing needs, selecting the right tools, and following a structured approach, manufacturers can overcome challenges and achieve significant ROI. Embracing AI is not just about adopting new technologies; it’s about creating a smarter, more efficient, and more resilient manufacturing future.